Day 1 :
Keynote Forum
Omar S Es-Said
Loyola Marymount University, USA
Keynote: Evaluation for long-term structural shading materials for use in harsh environments
Time : 09:20-09:50
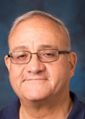
Biography:
Abstract:
This paper evaluated the performance and durability of leading structural shading materials to be used in the Super Containerized Living Units (Super-CLU’s) project. Fift een unique shading fabrics were tested in fi ve diff erent experiments in order to evaluate their strength, resistance to wind, abrasion, and heat and to assess their heat transmissivity and breathability. A current United States Navy material was used as a control material for the evaluation of the other tested materials. Samples of each fabric were fi rst tensile tested in both their warp and weft orientation to create an ‘as-received’ baseline condition. Th en, additional samples of each fabric were exposed to wind, abrasion, or heat and subsequently tensile tested to observe the change in tensile strength compared to the ‘as-received’ samples. Th e heat transmissivity and breathability testing was conducted separately
Keynote Forum
Augustin Gakwaya
University Laval, Canada
Keynote: Integrated forming processes and drop test simulations for a helicopter skid landing gear cross beam
Time : 09:50-10:20
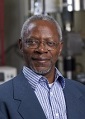
Biography:
Abstract:
Keynote Forum
Yun Li
Dongguan University of Technology, China
Keynote: Intelligent design and creativity for smart manufacturing
Time : 10:20-10:50
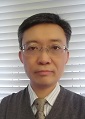
Biography:
Abstract:
- Special Session
Location: Amphitheater
Session Introduction
Colm M O’Kane and Robert Tully
Dublin Institute of Technology, Ireland
Title: Producing designers - development of DIT’s cross-disciplinary product design programme
Time : 11:10-11:50
Biography:
Abstract:
Agamenon R E Oliveira
Polytechnic School of Rio de Janeiro, Brazil
Title: Coulomb´s memoir on human-machine interaction
Time : 11:50-12:30
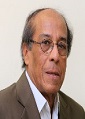
Biography:
Agamenon R E Oliveira has his expertise in mechanical engineering, mainly solid mechanics and in the last ten years in History of Mechanics. He is DSc in Mechanical Engineering (1982) as well as DSc in History of Sciences and Technology (2006), both by COPPE/UFRJ, Rio de Janeiro, Brazil. He published 80 papers and one book: History of the work concept- from physics to economics, by Springer (2013). He is member of IFToMM (International Federation for the promotion of Mechanism and Machine Science) and of SBHC (Brazilian Society of History of Sciences). He is also Professor of Mechanics and History of Technology at Polytechnic School of Rio de Janeiro, Brazil
Abstract:
- Design Engineering | Manufacturing Innovations| Materials Science | Production Engineering | Manufacturing Automation
Location: Amphitheater
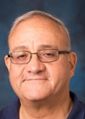
Chair
Omar S Es-Sai
Loyola Marymount University, USA
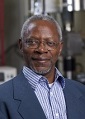
Co-Chair
Augustin Gakwaya
University Laval, Canada
Session Introduction
Nazim Mir-Nasiri
Nazarbayev University, Kazakhstan
Title: Human - exoskeleton interaction via tactile sensors for the motion assistance
Time : 13:40-14:05
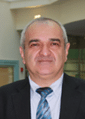
Biography:
Nazim Mir-Nasiri has obtained his PhD in Technical Sciences from Azerbaijan Technical University in 1989. Later he has built up his career in Malaysia as Head of Mechatronics Department at IIU Malaysia. From 2005 to 2013 he was holding a position of Professor and Head of Robotics and Mechatronics Program at the Swinburne University of Technology (branch of Australian University in Malaysia). Currently he holds a position of Professor and Head of Electrical and Electronic Engineering program at Nazarbayev University in Kazakhstan. He has published about 80 scientific papers in robotic design and control, machine vision, intelligent systems, design of mechanisms. He has received several awards at the International Competitions. In 2016 he has received NU Research Grant (USD 300,000). He is the member of IEEE for ten years and member of IMechE and UK Charted Engineer, Editorial Board Member of the “International Journal of Mechatronics and Automation” and “International Journal of Automation and Computing”.
Abstract:
The paper describes conceptual design and control of a new fully autonomous lower limb exoskeleton system via a number of tactile sensors. The aim of the exoskeleton is to support the subject weight and provide an additional strength and endurance for the subject. The designed exoskeleton can decouple the weight/mass carrying function of the subject/human from its forward motion function. This newly proposed approach effectively reduces the power and size of propulsion motors and thus the overall weight, cost of the system. The interaction between the system and subject takes place by means of two types of sensors. The system measures the pressure applied by the subject’s feet on the ground. If the pressure exceeds the set value the system blocks the motion at the knee joint by means of a passive air cylinder across the knee joint. This data is used by the PID controller to force the exoskeleton to follow precisely the motion of the subject legs in swinging motion by means of hip and knee motors. The mechanical structure of each leg has six degrees of freedom: four at the hip, one at the knee and one at the ankle. Only one degree at the hip and one at the knee are motor driven. In Fig. 1: 1 is a seat; 2 and 3 are hip and knee motors; 4 is an ankle join; 5 and 6 are bars to support the electronics and power supply;7 are leg belts; 8 is a hip lateral motion mechanism; 9 is an air cylinder.This exoskeleton is power efficient because the system motors are not used to support the subject weight like in most of the existing exoskeleton designs.
Jr-Rung Chen
Industrial Technology Research Institute, Taiwan
Title: Design and development of a step-gauge calibration system
Time : 14:05-14:30
Biography:
Jr-Rung Chen has completed his PhD from the National Taiwan University of Science and Technology. At present, he works at the Center for Measurement Standards of the Industrial Technology Research Institute. He has majored in three-dimensional metrology, precision engineering, and mechatronics.
Abstract:
A step-gauge, consisting of several short gauge blocks fixed on a base, is widely used in the calibration of machine tools and co-ordinate measuring machines (CMMs). The step-gauge calibration system is developed by comprising a laser interferometer and a CMM. The laser interferometer was used as the standard for traceability of length measurement and designed as a two-path interferometer system to decrease the Abbe error, and then integrated with the high-precision CMM, consisting of the moving platform and probing system to implement the calibration procedure for step gauge.
Maria Giulia Faga
National Research Council of Italy (CNR), Italy
Title: How to adjust the mechanical and biological properties of UHMWPE for biomedical purposes by changing the alumina-zirconia content
Time : 14:30-14:55
Biography:
Maria Giulia Faga is a Researcher of the National Research Council of Italy (CNR). Her research activity ranges from physico-chemical study of catalysts to the functionalization of massive materials (oxidic composites) for biomedical applications to the study of tribological and surface properties of wear resistant thin films for cutting tools. At present, she is responsible for the institute activity “Machining and characterization of materials for mechanical, wear resistance and biomedical applications” and responsible of the laboratories for mechanical and tribological properties of thin layers and bulk materials. Her research interests include the following laboratory skills: wear and mechanical characterisation of materials (tribometer, scratch test, durometers); microstructural (SEM-EDS) and spectroscopic (Raman, FTIR, UV-Vis, XRD) analysis. She cooperates mainly with the Chemistry group of University of Turin, the Materials and Machining Departments and the Department of Management and Production Engineering of Polytechnic of Turin.
Abstract:
Ceramic materials are widespread employed in biomedical application thanks to high strength and wear resistance. Among them, tetragonal ZrO2 shows bioactivity properties, although phase transition towards the monoclinic phase makes it unsuitable for biomedical applications. The problem has been solved by using ZrO2-Al2O3 composites, for which limited or absent phase transition is observed. However, similar biomaterials still present mechanical properties far to those of hard tissues. A possible strategy to overcome this issue is represented by the dispersion of alumina-zirconia composites in a polymer matrix. In such way it could be possible to obtain an implant easy to be processed, inexpensive, with suitable mechanical properties and good cells interaction. Polymer composites have also the advantage of a contrast adjustable radio-transparency and are compatible with modern diagnostic methods. In this work, different amounts of Alumina Toughened Zirconia (80–20 wt %) (ATZ) have been added to Ultra High Molecular Weight Polyethylene (UHMWPE). The UHMWPE/ATZ composites were prepared by solid state mixing, using a homogenizer, followed by compression molding. The structural, morphological, thermal, mechanical characterization and cells interaction of ATZ-UHMWPE are reported for the first time in order to assess the feasibility of these materials for biomedical tissue reconstruction.
In PE2.5 composite, ATZ particles are uniformly distributed along the ‘‘grain’’ boundaries, whereas at higher concentrations (10 and 20 wt %) they form micrometric agglomerates. The PE2.5 composite has improved elastic modulus and yield stress respect to bare UHMWPE. For all the other composites, an increase in the elastic modulus respect to neat UHMWPE is observed, although the other mechanical parameters are reduced by increasing ATZ content. The results can be explained in terms of poor dispersion of the oxide in the polymer matrix at concentrations higher than 2.5 wt %. Furthermore, the good dispersion of ATZ seems to positively affect the cells adhesion and protein adsorption (using Bovine Serum Albumin, BSA).
Miroslav Raudensky
Brno University of Technology, Czech Republic
Title: Flexible heat exchangers with polymeric hollow fibers
Biography:
Miroslav Raudensky is a Professor at Brno University of Technology. He is author or co-author of over 200 technical and research reports mainly for mechanical engineering and metallurgical industry. His main research interest is in experimental study of heat transfer, especially for high temperature and micro surface application. He has published over 70 papers in that field.
Abstract:
Polymeric hollow fiber heat exchangers were proposed about decade ago as an alternative to metal exchangers for low temperature application. Design of classical metal heat exchangers is limited by production technology. Majority of metal heat exchangers are of rectangular shape and the use of polymeric flexible materials brings new chance of production of light heat exchangers with almost arbitrary shapes. Two types of polymeric heat exchangers can be distinguished: The first is in the shape of chaotic bundle (Fig. 1) and the second is design with regularly separated heat transfer capillary (Fig. 2). Flexible polymeric hollow fiber heat exchangers were prepared and tested for liquid / air and liquid / liquid conditions. These heat exchangers use plastic capillary with outer diameter 0.5 - 0.8 mm and wall thickness 10% of outer diameter. These heat exchangers are flexible and can be used in narrow slots and in shaped channels. Experimentally obtained overall heat-transfer coefficients in water/air applications are up to 900 W/m2 K. These heat exchangers are effective even in natural convection application where advantage of high heat transfer coefficient on micro surfaces is used. The use of plastic and non-corrosive materials is advantageous in applications where weight of heat exchanger is important (about 50% reduction of weight in comparison to classical metal products) and in difficult chemical environment. The paper present results of laboratory tests of the developed prototypes of polymeric hollow fiber heat transfer surfaces of variety of designs.
Mahmut EkÅŸioglu
Bogaziçi University, Turkey
Title: Ergonomics in design: Safety and user experience factors
Time : 15:20-15:45
Biography:
Mahmut EkÅŸioÄŸlu is currently a Professor of Industrial Engineering and Director of Ergonomics Laboratory at BoÄŸaziçi University. He received his PhD in Industrial Engineering and MS degrees in Industrial and Aerospace Engineering all in the US and a BS degree in Mechanical Engineering in Turkey. His area of expertise is in Ergonomics/Human Factors Engineering and he has been working in this area since 1992 as an Instructor, Researcher and Consultant both in the US and Turkey. He published over 70 articles in SCI journals and conference proceedings as well as several book chapters and developed an ergonomics assessment tool. He is also the inventor of the patented Turkish E-Keyboard which is a Turkish Standard. He has memberships in several international professional societies.
Abstract:
Product/system design and development requires an interdisciplinary approach considering the lifecycles of products/systems. Traditionally, designers focus on functionality and perhaps economic aspects of the products/systems. However, safety of a product/system is also a very important factor that should be considered by the designers and modern engineers are required for this. Human life and health may be at stake and indeed, it is a liability issue as well. Most accident analysis reports indicate that accidents are related to human errors. However, careful analyses of such incidents reveal the real cause: Most of the accidents are due to equipment failure or design error. That is, human errors mostly originate from poor designs and for the case of user experience: the product should be useful, usable, findable, credible, desirable, accessible and valuable. The design stage offers the greatest opportunity and most cost-effective time to anticipate, analyze, eliminate, or control hazards, and examine and include the user experience aspects. Ergonomics is an applied science and engineering discipline concerned with these. In this paper, a critical examination of safety and user experience principles of product/system design and development is examined with examples from ergonomics perspective.
Biography:
Olga Kamynina, PhD Chemical Physics, is currently a Secretary for science at the Institute of Structural Macrokinetics and Materials Science, Russian Academy of Sciences (Chernogolovka, Moscow region). Her areas of interest include: Dynamics of phase and structure transformations during high-temperature processes in micro-heterogeneous systems; Mechanisms of combustion wave propagation in micro-heterogeneous media; Combustion synthesis of advanced materials; Product structure formation in conditions of combustion and thermal explosion; Influence of micro-gravity on combustion (SHS experiments in ISS); Dynamics and mechanisms of pore formation; New SHS-produced porous biomaterials.
Abstract:
Self-propagating high-temperature synthesis (SHS), or synthesis by combustion, is based on exothermic reactions between the elements and/or compounds. This technique is advantageous over existing processes by (i) no need for external energy supply, (ii) high reaction rates, and (iii) simplicity of facilities. SHS can be carried out in the mode of either layer-by-layer combustion or thermal explosion (volume reaction). The applicability of SHS method to fabrication of materials with desired properties was demonstrated in [1-4]. In this communication, I will report on some recent results on the combustion synthesis of Ti- and Ta-based materials. Due to unique combination of their properties, such materials are widely used in industry as structural and functional materials. This work aimed at exploring the feasibility of preparation of Ti–Al–Ta alloys from the elements in a mode of thermal explosion. In experiments, we studied the influence of the size/morphology of powders and mechanical activation of the powders on reaction mechanism and product patterning. Another goal was the deposition of multilayer ceramic Ti–C–Si coatings onto Ti and Ta substrates. Ti-Al-Ta-based alloys can be synthesized by thermal explosion without introduction of non-metal additives into the green mixture. SHS method can be readily applied to deposition of multilayer ceramic coatings onto a Ti and Ta substrate, without use of low-melting metal (intermediate layers). The use of SHS reactions for the purpose was found rather promising.
Kadiata Ba
University Laval, Canada
Title: Hot forging process simulation for aerospace aluminum alloy using a modified Johnson-Cook equation
Time : 16:30-16:55
Biography:
Kadiata Ba is a professor in mechanical engineering at the Université du Québec à Chicoutimi, in Québec Canada.
Abstract:
In the aerospace industry, parts requiring tight dimensional tolerances and very high mechanical properties are often produced by forging. This forming process allows for an optimal use of the material and can produce high quality parts at a reasonable cost. Thanks to CAD techniques, it is now easier to predict flow profiles and in-process defects occurrence as well as wear of the forging dies. However, in order to determine the properties of the forged part with computer simulation methods, a good material constitutive law is a prerequisite. This paper presents a virtual manufacturing process modeling for the closed die forging of a workpiece performed with Abaqus. The hot closed die forging is a regular process applied to manufacture metallic components used in aerospace industry. In this forming process, the material flow and final properties depend on the microstructure evolution during the process that is why it is important to include the microstructure effects in the material model. Based on the stress-strain data measured experimentally, the material parameters of the standard (classical) Johnson-Cook constitutive model and of a modified Johnson-Cook constitutive law including the microstructure effects have been determined. The obtained simulation results are compared with the experimental results for validation.
Kadiata Ba
University Laval, Canada
Title: Hot forging process simulation for aerospace aluminum alloy using a modified Johnson-Cook equation
Biography:
Kadiata Ba is a professor in mechanical engineering at the Université du Québec à Chicoutimi, in Québec Canada.
Abstract:
In the aerospace industry, parts requiring tight dimensional tolerances and very high mechanical properties are often produced by forging. This forming process allows for an optimal use of the material and can produce high quality parts at a reasonable cost. Thanks to CAD techniques, it is now easier to predict flow profiles and in-process defects occurrence as well as wear of the forging dies. However, in order to determine the properties of the forged part with computer simulation methods, a good material constitutive law is a prerequisite. This paper presents a virtual manufacturing process modeling for the closed die forging of a workpiece performed with Abaqus. The hot closed die forging is a regular process applied to manufacture metallic components used in aerospace industry. In this forming process, the material flow and final properties depend on the microstructure evolution during the process that is why it is important to include the microstructure effects in the material model. Based on the stress-strain data measured experimentally, the material parameters of the standard (classical) Johnson-Cook constitutive model and of a modified Johnson-Cook constitutive law including the microstructure effects have been determined. The obtained simulation results are compared with the experimental results for validation.
Dejan Šeatović
Dejan Šeatović, University of Applied Sciences, Germany
Title: Let machines do the work!
Time : 16:55-17:20
Biography:
Dejan Šeatović is an experienced Engineer and Scientist with strong focus on intelligent systems. Has led in numerous industrial and research projects which have shaped his competences in areas of software engineering, mechatronics, remote sensing, ranging and computer vision. His mission is to understand the end-user requirements and wishes in order to steer the research and development towards usable and reliable intelligent systems. His professional career started at Leica Geosystems AG, Switzerland and continued in the academic environment, where he is at present and effectively connects both worlds.
Abstract:
Within the last decade the performance of spatial data acquisition devices has increased to a level where, in a split second, several gigabytes of observation data can be acquired at once. With the increased performance of sensors, processing time and complexity of large amounts of data have increased as well. The employment of the human work force for data processing and analysis is expensive, and has limited capabilities. To transform data to information, automation procedures for segmentation, labeling and interpretation of acquired data are necessary to support human decision makers in generalization and information classification. Recent progress in machine learning, especially convolutional neural networks, the window of opportunity has been opened for assisting systems: They have chance to become more reliable and robust without additional implementation efforts. These new assisting systems are able to perform tasks which were reserved for trained human labor. Following two use cases should be considered: a) an intelligent and autonomous catheter, guided by highly accurate and reliable sensor-actor control system should be able to perform TAVI operations on a patient. b) An autonomous robot equipped with 3-D and multispectral sensing performs weed detection and treatment 24/7 without significant human assistance. These systems have great potential as products, though there are still various hurdles to be taken. Apparently, the state-of-the art deep learning methods can solve many of the challenges: They are able to crunch a large amount of data, extract useful information, and make decisions autonomously. At present these methods rely on very large amount of data that is required for their training. The crucial question is: Is there an efficient solution to improve the performance of intelligent systems with more accurate and reliable sensors? Reducing the noise in the measurements enables more efficient and precise modelling of the data, thus shorter training process. Is it that simple? Two use cases mentioned above were major goals in several successful research projects, their results allow interesting discussion.
- Young Researchers Forum
Location: Amphitheater
Session Introduction
Yogang Singh
University of Plymouth, UK
Title: USV navigation in a real-time map using intelligent path planner
Time : 17:20-17:35
Biography:
Yogang Singh joined Plymouth University, UK as a Commonwealth Scholar in PhD programme under School of Engineering in 2015. He has more than 6 years of research experience in area of CFD and Marine Robotics with a particular interest in Hydrodynamics. He has built an in house underwater glider at IIT Madras, Chennai (India) where he completed his MS (by research) in 2015. Prior to that, he worked as Research Assistant in Government of India projects for a period of two years. At present, he is working on developing path planning algorithms for Swarm of Surface USV. His goal is to combine CFD techniques in conjugation with real time operation of marine robots such as underwater vehicles and submarines.
Abstract:
Unmanned surface vehicles (USV) are the recent trend in marine robotics due to their diverse application and easy deployment. Navigation of such USV in a real time marine environment is a major challenge and creates a need towards development of intelligent path planners which can increase the system autonomy. Many such intelligent path planning studies have been conducted in the area of mobile robotics but needs a lot more research to be conducted in area of marine robotics. In this study, a well-known intelligent path planner A* has been implemented in a real time map using safety distance from obstacle as the criteria towards generating optimal trajectory for a single USV navigation. Different safety distances from obstacles ranging from 10 pixels to 40 pixels have been used to generate optimal trajectory and comparative performance has been analyzed in terms of computational time and path length. In this study, Portsmouth Harbour has been considered as area of study to determine the effectiveness of A* algorithm with different safety distance from obstacle as constraint. Algorithm has been validated on computer-based simulations using C++ and OpenCV libraries.
Farzad Hemmati
Farzad Hemmati, University of British Columbia, Canada
Title: Constrained design optimization using MATLAB & ANSYS: Assessment of accuracy & Hessian matrix assumptions
Time : 17:35-17:50
Biography:
Farzad Hemmati has his research mainly focused on dynamic characteristic problems of high-speed turbomachinery. Continuous online monitoring is necessary to assess health conditions, to enable early detection of operation problems and to reduce possibility of downtime. Destructive excessive vibrations in rotor supported oil film journal bearing systems are mainly caused by misalignment, unbalance, and oil-induced instability phenomenon known as whirl. In many of the published works, the predictions of the instability threshold speed and dynamic response of the rotor supported by fluid-film journal bearings are based on the linearized stiffness and damping coefficients. Nevertheless, the fluid forces generated in fluid-film journal bearings are highly nonlinear so that bifurcation exists around the instability threshold speed.
Abstract:
In this paper, a nonlinear constrained optimization problem is solved using MATAB’s Optimization Toolbox and ANSYS APDL’s Design Optimization. The objective is to investigate the accuracy of both methods and to assess the assumptions used in approximating the Hessian matrix in each case. The sequential quadratic programming (SQP) technique is applied through MATLAB and a subproblem approximation method using the sequential unconstrained minimization technique (SUMT) through APDL. SQP linearizes the constraints and solves the QP subproblem to form a line search to decrease the descent function whereas in SUMT the constrained problem is converted to an unconstrained problem using a transformation that applies a penalty function in place of the constraints. Comparing the two techniques it was found, based on the results that the sub problem approximation method from APDL proved more accurate since the optimum solution was a global minimum, whereas in MATLAB a local minimum result was obtained. The treatment of the Hessian matrix by the two techniques was studied in order to understand its effect on the results; the SQP method utilizes a quasi-Newtonian method, the BFGS method, to approximate the Hessian matrix while in APDL, no approximation is made since the subproblem approximation method is a zero-order method.
Xingyuan Wang
Dalian University of Technology, China
Title: Theoretical method for prediction of press-mounting force and stress distribution in assembly process of interference fits
Time : 17:50-18:05
Biography:
Xingyuan Wang is major in precision instruments and machinery. He is devoted to the assembly of small precision interference fitting parts and assembly quality estimation. His theoretical model for prediction of press-mounting force and stress distribution based on thick-walled cylinder theory provides a standard for quality estimation.
Abstract:
Statement of the Problem: Interference fit is widely used in many industrial fields for its high ability to transmit an axial force or torque between a shaft and hub. Thick-walled cylinder theory (TCT) is the main tool for analysis and design of interference fit. After many researches, theoretical methods based on TCT were more abundant and perfect, which can be adopted for complex structures and different operating conditions. However, the current theoretical system still has some shortcomings, such as the influence of non-contact regions on stress distribution and press-mounting force. Since the stress distribution and press-mounting force in the assembly process are significant for analysis of contact surface wear and assembly quality estimation, the purpose of this study is to build a new theoretical model to predict the stress distribution and press-mounting force.
Methodology: A simplified model was proposed by dividing the geometric model into three parts: contact region, non-contact regions of shaft and hub respectively. Then, the press-mounting force was calculated by the combination of the friction force generated by contact region and a resistant force generated by non-contact regions. The stress distribution equation was also deduced based on a simplified model that a non-uniform linear load acts on a portion of the semi-infinite plane.
Results: The theoretical results of press-mounting force were consistent with simulation results and validated by experiments. The prediction results of stress distribution were also compared with simulation results which indicate that the new theoretical model has high accuracy in stress distribution prediction.
Conclusion & Significance: The new theoretical model can give more accurate and reasonable results and provide a more reliable approach for designing of interference fits. Furthermore, this model also provides a method for improvement of the analytical method of interference fits under different structures and operating conditions..
- Mechatronics | Smart Materials and Technologies | Automation Engineering | Advanced Intelligent Mechatronics | Industrial Automation
Location: Amphitheater
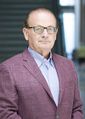
Chair
Andrew A Goldenberg
Chief Technology Officer SuperRobotics Ltd., Hong Kong, China ANZER Intelligent Systems Co. Ltd., Shenzhen, Guangdong, China Engineering Services Inc., Toronto, Ontario, Canada Professor Emeritus University of Toronto
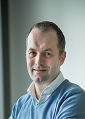
Co-Chair
Christian DurieZ
INRIA, France
Session Introduction
Matthias Wimmer
Munich University of Applied Sciences, Germany
Title: A semi-sequential actuator design for multipoint tools
Biography:
Matthias Wimmer is a Postgraduate Research Student at Plymouth University and a Research Assistant at Munich University of Applied Sciences. His research is focused on reconfigurable tooling technologies in general and multipoint tooling in particular. In his PhD, encompasses the optimization of critical components within the multipoint tooling systems. He has published articles in reputed journals and presented at international conferences.
Abstract:
Multipoint tooling is a reconfigurable mold making technology that replaces solid moulds with an array of individually adjustable pins to create a discrete representation of the desired mould geometry. These pins have to be adjusted to very precise heights in reasonable time with manageable tool complexity to create a competitive new technology. Leadscrew driven pin actuation has proven to be precise, reliable and cost efficient. The height adjustment of the individual pins thereby can be either direct, with dedicated drives for each pin, or sequential, with one actuator used for all pins. A semi-sequential adjustment design is introduced to combine the advantages of both these designs. The passive, sensor less, pins in this concept are adjusted with an array of actuator devices. A setup algorithm ensures precise adjustment of each pin. The connection between the pins and the actuators is realized with a specifically designed form lock claw clutch. To ensure reliable function of this clutch the coupling process and parameters influencing coupling performance are analysed. Different methods of measurement are tested and evaluated to ensure the coupling’s performance. Subsequently sensitivity analysis is used to evaluate the influence of each parameter on the coupling performance and create a reduced parameter set. A Metamodell of Optimal Prognosis (MOP) is derived and used to optimize the actuator parameters. Finally, the robustness of the optimized system is tested. After parameter optimization, the design operates reliable and can reduce the total costs of a multipoint tool significantly.
S P Tewari
Indian Institute of Technology (BHU) Varanasi, India
Title: Influence of mold oscillation during solidification on grain size, degree of grain refinement and tensile properties of the A356 and A319 aluminum alloys
Biography:
Dr..S.P. Tewari has his expertise in casting and welding area . He is having approximately 37 years of teaching and research experience in the area of casting and welding. He has published more than 60 research papers in international and national journals. He has authored six books in the field of manufacturing and production engineering. His extensive work is in the area of mold oscillation and weld pool oscillation which bring about grain refinement and ultimately leads to the enhancement of mechanical properties of casting and weldments respectively.
Abstract:
A356 and A319 aluminum alloys were cast under stationary and oscillation condition. The frequency range selected was 0 Hz to 400 Hz with constant amplitude of 15 μm. It has been observed on the basis of experimental results that intensity of oscillation, in general enhances mechanical properties such as ultimate tensile strength, yield strength and percentage elongation of casting along with reduction of grain size of α-Al. The mechanical and metallurgical properties are appreciably improved at a higher frequency of oscillation. This may be due to the increase in number of nucleation sites because of fracturing of grains due to oscillation. Rapid ejection of heat of molten metal takes place due to mold oscillation at interface during solidification. This brings about grain refinement and modification of eutectic cells in casting.
Amirat Abdelaziz
Badji Mokhtar University of Annaba, Algeria
Title: Advanced concept in analysing tool performance in parts production processes
Biography:
Amirat Abdelaziz has completed his Bachelor’s in Engineering in Production Engineering; MSc Research and PhD in Mechanics of Materials. He is a Professor since 2009 in Badji Mokhtar Annaba University and has been leading a research team in new materials and composite in the mechanics of material and plant maintenance laboratory and then recently a new team in internal logistics in production workshops, in the laboratory of advanced technology in production engineering. He has been President of the national committee of the professional branch of mechanical and steel industry, within the ministry of vocational training of Algeria for 4 years. He is a member of MasTech Tempus Project and he has published papers in reputed journals and attended international conferences.
Abstract:
Despite the efforts that are continuously spent in developing high technology to make the production engineering process accurate, reliable, efficient and competitive, there is stil a great deal with lifetime of the tools involved as they are always subjected to progressive damage because of plastic deformation, wear and cracking. Unpredictable failure of tools has great effect on the production and non-maintenace costs. The present work introduces an advanced concept in analyzing tool performance in parts production processes. The concept is based on an engineering model developed by coupling the process behavior model and a corresponding damage model. The analyses uses reliability approach that permits to determine a reliability index expressed in terms of number of parts produce with the same tool regarding the required quality and safety. The higher the number of parts the better the performance of the tool. So the concept will be developed and applied to two case studies: forging die and cutting tool. In both cases the performance index is expressed as the number of produced parts before changing tools because respectively of fatigue damage and wear. A particular attention is given to the uncertainties associated to the variables involved in the mechanichal engineering models in order to analyse their sensitivity.
Xiaodong Wang
Dalian University of Technology, China
Title: Quality estimation of interference fits assembly based on press-fit curve
Biography:
Xiaodong Wang has his expertise in precision assembly and automation in improving the assembly quality and efficiency for miniature devices. Currently his research work includes analysis of assembling process, design and manufacture automatic measuring instruments and assembly equipment for production of miniature devices. He has won the China Mechanical Science and Technology Award and China Aviation Industry Group Corporation Technology Award in recent years for his achievements in precision assembly technology and system development. He developed a variety of automatic assembly equipment and provided assembly solutions for research institutes and companies. He holds over 30 China invention patents in related research work.
Abstract:
Statement of the Problem: Press-fit assembly is one of the traditional methods for assembly of interference fitting parts, and its assembly quality has attracted the attention of many researchers. Generally, the strength of assemblies depends on various parameters such as interference value, physical dimensions, form error of contact surfaces, etc. Furthermore, the connection quality cannot be obtained directly by the press-fit method. Hence, many studies have been performed to investigate the effect of various parameters on the load bearing ability of interference fits based on finite element method (FEM) and theoretical method. But most of the researches focus on the contact status of finished interference fits. Since the press-fit curve can be used for real-time monitoring and evaluate the assembly quality, the purpose of this study is to obtain standard press-fit curves as an evaluation criterion to estimate the assembly quality.
Methodology: A theoretical model and simplified FE model were used to predict the standard press-fit curves. To verify the accuracy of the prediction results, assembly experiments were carried out using an automatic press-fit instrument which consists of binocular vision device, upper and lower fixtures, XY precision stages, and force-displacement measurement module, etc. Finally, the reasonable growth tendency and a reasonable range of maximum press-mounting force are obtained and used for quality estimation.
Results: The prediction results of the press-fit curve have sufficient accuracy, and the evaluation strategy proposed in this study can give a reasonable assessment of assembly quality whether the failure is caused by form error or alignment error, etc.
Conclusion & Significance: The theoretical model is more efficient than FEM in press-fit curve prediction. The evaluation strategy can be used to predict the assembly quality, which is of great significance to improve the reliability of interference fits.
Ibrahim Gadala and Mohamed Gadala
University of British Columbia, Canada & Abu Dhabi University, UAE
Title: An automated system for the design and optimization of industrial motion control machines: development and case study
Biography:
Ibrahim Gadala is currently an Integrity Specialist with the Encana Corporation in Calgary, Canada. He graduated with PhD in Materials Engineering in 2017 from the University of British Columbia in Vancouver, Canada. He has a background in Mechanical Engineering Design and Optimization through his Master’s thesis research. His research interests include materials characterization, pipeline integrity, mechancial design, optimization, and automation. He has recently been an Erasmus Mundus Visiting Researcher at Ghent University in Belgium and a Sessional Instructor of various Materials/Mechanical Engineering courses at UBC Vancouver.
Abstract:
Motion control is a form of automation which enables the position- or velocity-control of a machine using an actuator such as an electric motor. The selection of suitable components and actuators for complex mechanical structures requires significant engineering expertise and intelligence. In this work, a design expert system is presented to support and automate the motion control system design process through optimization of the mechanical components involved and accurate selection of an actuator-transmission combination for the system. The design expert system contains an optimization and motor selection knowledge base, is synchronized with Matlab® optimization schemes, and is linked with Excel® spreadsheets of purchasable motors and gearheads. Specifications and anticipated performance data of selected drive models are provided for each design expert system decision. Verification of the developed system is conducted on an industrial conveyor belt. A culminating case study involving a heavy-weight industrial hoister driven by a DC motor is presented, where the developed automated system is found to consistently outpace human performance on the same design tasks.
Hao-Ting Lin
Feng Chia University, Taiwan
Title: Develop the path planning system for a B-axis fixed plane on a 4-axis machine tool
Time : 15:10-15:35
Biography:
Hao-Ting Lin is an Assistant Professor of Mechanical and Computer-Aided Engineering, Feng Chia University and he received his PhD degree from National Taiwan University in 2012. Between 2013 and 2015, he was a Postdoctoral Fellow in Graduate Institute of Oral Biology and Department of Engineering Science and Ocean Engineering in National Taiwan University. In 2015, he began as an Assistant Professor in Feng Chia University in Taiwan. His research interests include Dynamics Analysis and Simulation, Robotics, Mechanical Design and Analysis, Microfluidic Application, Bioengineering and Medical Device.
Abstract:
In this paper, a path planning system for B-axis is developed for a 4-axis turn-mill multitasking machine. Due to the lack of B-axis, the features on a tilt plane are difficult to be machined; this research developed value-added software to solve above issues. Extending the machinability of a CNC multi-axis machine tool can be achieved without increasing cost, this research uses homogeneous coordinates to transform the existing 3-axis machining path which planned in the system into a tilt fixed plane machining path. In addition, the theoretical formula of bottom surface roughness is derived from the research, and C♯ programming language and Visual Studio platform are utilized to complete the development of HMI (Human-Machine Interface). Four machining paths and the prediction of roughness are the main features for this tilted plane machining software. The HMI is primarily presented in a dialog form so that the users have a simple operating environment which is a low threshold of technique. This software is mainly used in aerospace, automobile, and precision machinery industries. Set each machining path into a path-function of C♯ language, and set homogeneous coordinate matrices into a method of C♯ language to apply to each coordinate point. In order to transform a horizontal plane to a tilt plane, the program needs the rotation matrix by the world Y-axis and the rotation matrix by the current X-axis. Also, the prediction of roughness is derived from the bottom milling. Verification of the software which is developed in this research is done through NcPlot, Vericut, and AutoCAD, by testing the accuracy of the path of the exported program, the accuracy of the path is less than or equal to 1 μm. In order to enhance the practicality, researcher derives a new formula for predicting the surface roughness, the rate of error for predicting is less than 10%. Finally, the speed of generating machining code is 92.8% faster than a traditional method.
Parinya Anantachaisilp
Royal Thai Air Force Academy, Thailand
Title: Fractional order PID control of rotor suspension by active magnetic bearings
Biography:
Parinya Anantachaisilp received his PhD in Electrical Engineering from University of Virginia in 2015. He is now teaching at the Royal Thai Air Force Academy. His research interest includes control design system, fractional order control, active magnetic bearings, rotating machinery, unmanned aerial vehicle, and mechatronics.
Abstract:
One of the key issues in control design for Active Magnetic Bearing (AMB) systems is the tradeoff between the simplicity of the controller structure and the performance of the closed-loop system. To achieve this tradeoff, this talk proposes the design of a fractional order Proportional-Integral-Derivative (FOPID) controller. The FOPID controller consists of only two additional parameters in comparison with a conventional PID controller. The feasibility of FOPID for AMB systems is investigated for rotor suspension in both the radial and axial directions. Tuning methods are developed based on the evolutionary algorithms for searching the optimal values of the controller parameters. The resulting FOPID controllers are then tested and compared with a conventional PID controller, as well as with some advanced controllers such as Linear Quadratic Gausian (LQG) and H-infinity controllers. The comparison is made in terms of various stability and robustness specifications, as well as the dimensions of the controllers as implemented. Lastly, to validate the proposed method, experimental testing is carried out on a single-stage centrifugal compressor test rig equipped with magnetic bearings. The results show that, with a proper selection of gains and fractional orders, the performance of the resulting FOPID is similar to those of the advanced controllers.
Biography:
Hao-Ting Lin is an Assistant Professor of Mechanical and Computer-Aided Engineering, Feng Chia University and he received his PhD degree from National Taiwan University in 2012. Between 2013 and 2015, he was a Postdoctoral Fellow in Graduate Institute of Oral Biology and Department of Engineering Science and Ocean Engineering in National Taiwan University. In 2015, he began as an Assistant Professor in Feng Chia University in Taiwan. His research interests include Dynamics Analysis and Simulation, Robotics, Mechanical Design and Analysis, Microfluidic Application, Bioengineering and Medical Device.
Abstract:
In this paper, a path planning system for B-axis is developed for a 4-axis turn-mill multitasking machine. Due to the lack of B-axis, the features on a tilt plane are difficult to be machined; this research developed value-added software to solve above issues. Extending the machinability of a CNC multi-axis machine tool can be achieved without increasing cost, this research uses homogeneous coordinates to transform the existing 3-axis machining path which planned in the system into a tilt fixed plane machining path. In addition, the theoretical formula of bottom surface roughness is derived from the research, and C♯ programming language and Visual Studio platform are utilized to complete the development of HMI (Human-Machine Interface). Four machining paths and the prediction of roughness are the main features for this tilted plane machining software. The HMI is primarily presented in a dialog form so that the users have a simple operating environment which is a low threshold of technique. This software is mainly used in aerospace, automobile, and precision machinery industries. Set each machining path into a path-function of C♯ language, and set homogeneous coordinate matrices into a method of C♯ language to apply to each coordinate point. In order to transform a horizontal plane to a tilt plane, the program needs the rotation matrix by the world Y-axis and the rotation matrix by the current X-axis. Also, the prediction of roughness is derived from the bottom milling. Verification of the software which is developed in this research is done through NcPlot, Vericut, and AutoCAD, by testing the accuracy of the path of the exported program, the accuracy of the path is less than or equal to 1 μm. In order to enhance the practicality, researcher derives a new formula for predicting the surface roughness, the rate of error for predicting is less than 10%. Finally, the speed of generating machining code is 92.8% faster than a traditional method.
- Video Presentation
Location: Amphitheater
Session Introduction
Hiral H Parikh
Navrachana University, India
Title: Experimental investigation and prediction for tribo behavior of fillers concentrated FRP
Biography:
Hiral H Parikh has pursued her PhD from CHARUSAT, Changa University, Gujarat, India, in the field of Tribological Characterization of Polymer Matrix Composites. Her research interest areas are biodegradable composites, polymer and polymer composites, tribological characterization, adhesive and abrasive wear analysis. She has guided many undergraduate projects and two postgraduate projects and she is a recipient of Dean’s Choice Award - 2015 at Navrachana University, she serves as an external examiner to evaluate undergraduate students at various universities. She is accomplished researcher authored several research papers which have been published in national and international conference proceedings. She is the author of two book chapters with Springer and ACME (Advances in Chemical and Mechanical Engineering) publishers. She has number of international journal publications in her credit. She is also a member of Tribology Society of India and Indian Society of Technical Education.
Abstract:
Composites have been established as one of the most promising modern materials to replace conventional metals and alloys in numerous structural and tribological applications. Fiber reinforced polymer (FRP) materials developed using thermoplastic and thermosets as matrices, natural and synthetic fibers as reinforcing and organic and inorganic materials as fillers have potential owing to their high strength to weight ratio. Natural fiber reinforced materials developed using plant fibers have attached the attention of the manufacturers because of their good strength, low cost and biodegradability. In the present work, cotton fibers are used as reinforcement with the polyester resin material. Tribological characterization of a material, determines its wear and friction coefficient properties at different operating parameters such as load, sliding distance, sliding velocity, filler content, etc. Response surface Box Behnken (BB) design approach is used to create the design matrix. Scanning electron microscope (SEM) is used to investigate the morphology of worn surfaces and artificial neural network (ANN) has been used to predict the tribo behavior of the cotton fiber polyester composites. A measured experimental database was used for successful training of the ANN and the test results reveal that the fillers have significant effect on tribo behavior of cotton fiber polyester composites. The results of validation network show that predicted tribo behavior is well acceptable when comparing it with the actual experimental results. The use of cotton fiber reinforced polyester composites can be employed depending upon various applications as per the requirement. For instance, the materials offer low wear rate and low co-efficient of friction may be used for the mechanical elements like gears, seals, bushes, bearings and turbines. The materials which offer high co-efficient of friction and low wear rate may be used for the brakes and clutches.