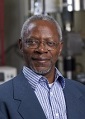
Augustin Gakwaya
University Laval, Canada
Title: Integrated forming processes and drop test simulations for a helicopter skid landing gear cross beam
Biography
Biography: Augustin Gakwaya
Abstract
In this work, a new helicopter skid landing gear cross beam is presented. Th anks to a revisited design, this part can be easily fabricated by tube hydroforming. Th e strength and energy absorption during emergency landing are the same for the new crosstube and for the actual crossbeam, but the new design is lighter. Th e manufacturing process is also “greener” and more cost-eff ective than the chemical milling process currently in use. For a better assessment of the structural integrity of the aerospace components, a methodology based on the integrated computational material science and engineering (ICME) technology for the multistage manufacturing processes of a helicopter skid landing gear component is used. Simulations of the manufacturing sequence and drop test are performed in an integrated manner. Th e tube is fi rst bent, then crushed and hydroformed. Aft er hydroforming, the tube has to be heat treated to bring the material into an artifi cially aged condition. Th e fi nal material properties depend on the amount of plastic strain experienced by the material during the forming processes, which varies from one part of the tube to another. Th is is taken into consideration for the simulations of drop tests and quasistatic loading of the part. Results from the simulations are compared to experimental results for bending, hydroforming, and quasi-static loading. By combining targeted physical testing with advanced materials and process modeling, the product design and manufacturing process can be optimized together at the early stages where cost of design changes is much lower. A better understanding of what happens to the material during the various processes and how to improve them can thus be achieved and the design engineers are enabled to optimize the component while maintaining security margins.