Day 1 :
Keynote Forum
Stephen G R Brown
Swansea University, UK
Keynote: Rapid alloy prototyping for steels
Time : 09:20-09:55
Biography:
Stephen G R Brown is Head of the College of Engineering at Swansea University, Wales, UK. His current research work involves modelling and experimentation for additive manufacturing, alloy discovery and high-throughput testing for high entropy alloys and steels.
Abstract:
Steel is the most widely used structural material in the world. Innovations in alloy development contribute to advances in key manufacturing sectors including automotive, packaging, defence and construction. Globally the development of new steel and coating alloys is a slow and iterative process involving significant business risk and expensive trials of many 100s of tonnes. This paper describes a high throughput approach to trials where substantial numbers of small scale samples will be prepared and their properties and processability tested and modelled using state of the art imaging, computational modelling and mechanical testing. This effort is a new partnership between Swansea University, Warwick University and Tata Steel. The research direction is informed, but not limited, by the pull from customer requirements, future product projections and by existing constraints introduced by processing asset limitations and residual elements contained within scrap, an essential component of all primary steel. This radical virtual factory approach will be integrated into a scale up activity enabling the simultaneous solution of new materials invention and processing. This research has the potential of transforming the steel innovation cycle and reducing screening times by a factor of up to 100 creating a vibrant 21st century steel manufacturing industry, feeding a diverse supply chain operating in multiple sectors.
Keynote Forum
Tsuyoshi Setoguchi
Hokkaido University, Japan
Keynote: Architectural design with climate using snow and wind simulations to prevent from snowstorm in winter cities
Time : 09:55-10:30
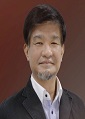
Biography:
Tsuyoshi Setoguchi is the Professor, Vice-Dean of Faculty of Engineering, Hokkaido University that is the northernmost major university in Japan. He has published more than 50 papers in reputed journals and got several prizes on these thesis as follows, Prize of Architectural Institute of Japan (AIJ) (2014), Prizes for Science and Technology by the Minister of Education, Culture, Sports, Science and Technology (2015) and Prize for Country development technology by Minister of Land, Infrastructure, Transport and Tourism (2016). He designed Wakkanai Station which is the northernmost station in Japan that prevent from snow and wind impact with his research technology.
Abstract:
Urban designs that should be symbiosis with regional environment and consider regional climatic conditions are one of the most important approaches for developing sustainable cities. Winter cities that suffer from heavy snow and cold winds in winter, an urban design approach different than that used for warm cities should be used. An urban design which reduces snow impacts is one of the most important approaches in heavy snow and cold climate cities. In this paper, the author evaluated the urban design for the new Wakkanai Station redevelopment project in Hokkaido, Japan. Wakkanai city is the northernmost city of Japan and located in a strong snowstorm area. A new design approach was required to be developed on the design process that should be combined architectural design and environmental engineering. From the architectural designing process, two types of alternative Wakkanai station design, the trapezoid type and the curved-surface type were addressed in the first stage. In next environmental engineering stage, both types were tested in snow simulations using a wind tunnel. Comparing those two types of design, the trapezoid type is better suited to alleviate the negative impact of snowdrifts on the pedestrian pathway. The formation of snowdrifts in the public areas is less likely to occur due to obstructions, and there is better access for passenger transfer and better approach for public bus and private vehicles. But some provision for the shelter of pedestrians from strong wind should be included in the redevelopment plan. The results of this environmental engineering stage were reflected to back the architectural design stage again in the Wakkanai station redevelopment project. Finally, the station design was decided and approved to the trapezoid type as the photo. Author developed the new urban design approaches with snow simulations. It might provide the most progressive design approach “design with engineering”.
Keynote Forum
Jose M Pardor Gortor
The University Carlos III of Madrid, Spain
Keynote: Screw Theory for Robotics - A modern mechatronics mathematical foundation
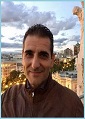
Biography:
Jose M Pardos Gotor has an extensive international career in the energy industry. He works for the Spanish utility ENDESA and has developed projects in Europe and Latin America in the fields of: Change Management, Sustainability, Electric Vehicles, Business Model Generation, Innovation, R&D, Commodity Markets & Trading, Energy Management and Power Generation. He is an Associate Professor in the Department of Systems Engineering & Automation at the UC3M (Universidad Carlos III de Madrid). His teaching and research areas are focused on production systems, industrial automation and robotics.
Abstract:
The importance of screw theory in robotics is recognized, but in practice, not many teach it to engineering students. Only few postgraduates know how to exploit it. However, in a variety of areas of robotics, the methods and formalisms based on the geometry and algebra of the screws have proven to be superior to other techniques and have led to significant advances recognized by robot researchers. Many say that kinematics for robots of many degrees of freedom (DOF) can only be addressed in a practical way with numeric algorithms. However, this approach is not very suitable for real time applications. Screw theory paves the way for solving kinematics with very compelling computational geometric algorithms truly effective and efficient, even for mechanisms and robots with many DOF. Using the product of exponentials, it is possible to develop geometric algorithms to solve the inverse kinematics problem. This method was originally presented by Paden and built on the unpublished work of Kahan. It is possible to develop additional problems to solve the inverse kinematics of different robots. For instance, the author presents some Pardos-Gotor (PG) canonical subproblems useful for solving prismatic joints. Several examples with applications to real industrial robots will be presented with MATLAB-Simulink-Simscape simulations and videos.
Keynote Forum
Petra Amparo López Jiménez
Universitat Politècnica de València, Spain
Keynote: Pumps working as turbines as an engineering solution for energy recovering in water distribution systems
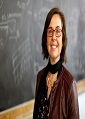
Biography:
Petra Amparo López Jiménez is an Industrial Engineer at the Universitat Politècnica de València and PhD in the Department of Hydraulic and Environment Engineering (DIHMA) of the same university. At present she is Full Professor of Hydraulic Engineering at the Higher Technical School of Industrial Engineering (ETSII) of the UPV and Director of the DIHMA. Her teaching experience is wide, since 1997 she has taught in the ETSII in aspects of fluid mechanics, hydraulic machinery and dispersion of pollutants, being also her main areas of research. She is Director of 7 doctoral theses and a multitude of final works of master and degree. She has worked in more than 50 projects or research contracts and is author of 85 articles in magazine, among other teaching and research contributions in congresses and conferences.
Abstract:
At present, the society has become aware of the need to increase the energy efficiency of all the processes in which it is involved. Therefore, the use of renewable energy sources such as photovoltaic, wind, tidal, hydraulics among others is necessary in order to increase sustainability. Water distribution systems should not be oblivious to this trend, especially if one takes into account that these nets are large consumers of energy. In this sense, hydraulic is a renewable source of energy with a promising future, furthermore there is a very important recovery energy potential in our water distribution networks. This energy is partially lost on valves, which main goal of these systems is the control of the network, but pressure is reduced without recovering the inherent energy of this additional pressure in the system. Therefore, it is of paramount importance to adjust the pressure in irrigation or potable water distribution systems for consumption, but considering the possibility of recovering this energy by implementing some engineered system to do so. If these pressure reducing valves are replaced by pumps working as turbines (PATs) not only can pressure regulation be achieved, but also some kilowatts can be recovered, that otherwise would not be obtained. The operation of pumps as turbines requires considerations in the design of the machines. What in pump conditions is an inlet in turbine conditions is an outlet, and vice versa. This makes important changes in the velocity triangles occurring in the impeller, and therefore the total behavior of the machines achieve different performance. Nowadays, the determination of real curves is crucial, considering hydraulic losses inside the machines and different rotation speed for the current researches. The knowledge of these curves will help to develop real models, which determine the final efficiency of different PATs.
Keynote Forum
Ludmila Kucerova
University of West Bohemia, Czech Republic
Keynote: Microstructure analysis of maraging steel X3NiCoMoTi 18-9-5 produced by additive manufacturing
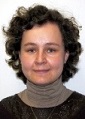
Biography:
Abstract:
Maraging steel X3NiCoMoTi 18-9-5 could be processed not only by conventional casting and heat treatment, but also by additive technology of laser direct melting. Input material for used selected laser melting (SLM) technology is metal powder. The powder used for additive manufacturing was analyzed to determine distribution of alloying elements within individual powder grains. Microstructure and mechanical properties of SLM build were determined in as-printed state and also after printing and subsequent heat treatment by either solution annealing or precipitation hardening. The microstructure in as-build state consisted of very fine cells of solid solution with thin films of retained austenite placed at the cell boundaries. An average tensile strength of 1050 MPa and total elongation of 8% was obtained in these samples. Solution annealing led to complete transformation of retained austenite to martensite and disappearance the original cellular microstructure. The resulting tensile strength was slightly below 1000 MPa, accompanied by total elongation of 9% and hardness of 328 HV 0.1. Precipitation hardening of as-built samples resulted in partial dissolution of the cells and an increased volume fraction of austenite. The ultimate tensile strength of hardened samples was nearly twice as high as in the as-built state reaching 1800 MPa. The microstructures and mechanical properties were compared with conventional maraging steel with the same chemical composition, sold under commercial name Vaco 180. In-situ observation of the straining of maraging steel in as-build condition was carried out, demonstrating the effect of metallurgical defects on failure initiation in additive manufactured steel.
- Design Engineering | Industrial Design | Manufacturing Process | Materials Science | Mechatronics Robots Applications of Automation | Human Robot Interaction | Control Systems
Location: Bolshoi
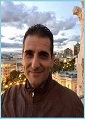
Chair
Jose M Pardor Gortor
The University Carlos III of Madrid, Spain
Co-Chair
Stephen G R Brown
Swansea University, UK
Session Introduction
Edith Bianchi
Business Development & International Sales Manager, Israel
Title: S2T (Skin-to-Thing) solutions for design & engineering R & D: what wearable device developers must consider for their IoMT device?
Biography:
Edith Bianchi has her background combining both clinical record as a Clinical Research Associate and Registered Nurse with CICU (Cardiac Intensive Care Unit) experience, as well as strong business management orientation with an MBA Degree from University of Derby (UK). She is a Senior Global Business Development Expert, specializing in the medical device industry – specifically in digital health and wearable applications. She has a long track international record in medical device firms and is a key person in few meaningful strategic cooperations between major global players in the industry. She has coined the term S2T (Skin To Thing) and continuously promotes patient's and users' human factors.
Abstract:
The internet of things (IoT) is allowing collected data from "things" to be connected to the cloud, where artificial intelligence (AI) can be used to identify trends and enable decisions to be made accordingly. This platform has been integrated into the medical field and is known as the internet of medical things (IoMT). This shift can potentially transform medical field as we know it today. By using this platform, we can generate and analyze the collected medical data in a way that was not possible otherwise. This holds a tremendous value to improve patient personalized care. It also carries the potential of creating an efficient way of health monitoring, promoting wellbeing, allowing real-time interventions, progress treatment and adherence and improving the management of chronic disease. IoMT devices are often presented in a concept of a wearable device and mobile healthcare applications. These devices are enabling and enhancing possibilities of home-care as well as access to medical experts anywhere. In a world with aging population and massive health expenditures, IoMT may be the very desired mean to cope with many of the challenges. Analysts are estimating the IoMT market to continue its growth trend and simultaneously the worldwide wearables market continued its upward trajectory. The starting point of every wearable medical device is always the patient. Whether it is a monitoring device, a diagnostic system, a drug delivery infusion pump or a nerve stimulation tool - in most cases the device would be attached to the skin. The patient's "Skin" interface to the "Thing", has been described in the term S2T (Skin-to-Thing). This crucial element is often overlooked by medical device developers, left for a later stage of design although at times, it may be the determining factor of implementation of the entire device or technology. Most of the focus of IoMT is rightfully directed to the device itself, to the computing and cloud technologies, to the electronics and to the gateways apps of the data. Yet, engineering teams must be aware of S2T and assume responsibility to understand its challenges and acquire the necessary expertise that is required for their specific skin-to-thing solution. The intended wearing location, duration, target population and many other considerations, should dictate the solution, its components and design. Indeed, engineering teams are becoming more and more familiar with factors that are critical to S2T ("Skin to Thing") required solution and its challenges to adhere the device to the patient's skin. Challenges such as biocompatibility and regulation requirements, the possible material interactions due to manufacturing technologies and comfortability to the end user – these aspects of body/machine interface should be given their deserved attention in order to assure the successful usage and benefits of current technological breakthrough is medical device, fitness, healthcare & pharmaceuticals industries.
Ali Kanso
Zentrum für Mechatronik und Automatisierungstechnik gemeinnützige, Germany
Title: Position and orientation calibration of a 2D laser line sensor using closed form least-squares solution
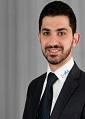
Biography:
Ali Kanso is a Scientific Researcher at ZeMA. His activities cover different fields in the frame of automation and handling devices. These are analysis and optimization of handling device, calibration of the robot kinematic chain and deployment of sensitive robots in the production.
Abstract:
Laser line sensors are used for inspection, positioning and scanning of 3D objects. They are often mounted on the flange of an industrial robot. The laser line sensor provides 2D measurement values in the x and z direction with respect to the sensor coordinate frame. In order to transform the measured values into the robot coordinate frame and therefore expand the 2D measured values into 3D coordinates, the position and orientation of the sensor coordinate frame with respect to the flange coordinate system must be determined by solving a kinematic equation in terms of transformation matrices. This article provides a complete solution for solving this problem. A unique solution is derived based on the separable closed-form solution after two movements of the robot flange under satisfying constraints. Robotic applications are usually implemented with the presence of noise. Therefore, a least squares solution is determined after performing several measurements. Finally the calibrated laser line sensor is integrated in combination with a process tool into a semi-automated assembly process in aircraft production. In the assembly of the aft section of the aircraft the pressure bulk head must be mounted through a riveting process to the section barrel. Using skills of humans and robots the riveting process can be performed precisely in human robot collaboration.
Fang Bin Guo
Liverpool John Moores University, UK
Title: Shifting product design from technology driven to user centre design
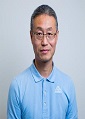
Biography:
Abstract:
Traditional industrial design is about functions and forms. Designers placed great emphasis on forms and aesthetics. However, technology innovation has shifted industrial design from the stage of technology driven to user centered design driven, this is also due to the functions of products are increasingly complex to interact, i.e. electrical/computers devices, mobile phones and multifunctional products. So that industrial design now emphasizes on bettering user experience. Don Norman defines user centered design as all aspects of the person’s experience with the system including the interface, the physical interaction and the manual. Technology revolution results in products are getting more complex, in particular those of multimodality interfaces include car dashboard and aircraft cockpits that displayed a number of information such as engine temperature, fuels level, speed etc. That challenges the user to recognize/understand the information. Human factor is the scientific discipline that concerned with the understanding of the interactions among humans and other elements of a system. The knowledge, in particular product semantics is a language that helps people to understand and interact with products easily and efficiently. Designers rely on this language to communicate with users; to express functions, reliabilities and characters through forms, material/textures and semiotics. This paper discusses user centered design and human factors knowledge, in particular product semantics and its application in product design; and reviewing a curriculum developed particularly focuses on user centered design within a BSc product design engineering programme.
Alec Burns
University of Liverpool, UK
Title: Precision material deposition via a mobile rover for disaster scenarios
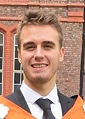
Biography:
Alec John Burns received his bachelor’s degree in Aerospace Engineering in 2016 from the University of Liverpool. From June 2015 to August 2015 he was a Research Assistant on a joint project between the Department of Earth, Ocean and Ecological Sciences and the Engineering Department at the University of Liverpool, working on fluid flow analysis for magma chambers. Currently he is pursuing his PhD at the University of Liverpool. His fields of interest include sensing, robotics and autonomous systems.
Abstract:
The most dangerous hazards in the aftermath of environmental disasters are typically linked to the damage that has occurred to structures. A material extrusion device capable of traversing highly irregular terrain, able to operate in hazardous or difficult to reach locations, and repair damage would largely mitigate many of the risks for survivors and relief workers. In this work, we propose a platform capable of tackling such challenge: a mobile tracked rover (MTR) that can travel on difficult terrains and deposit material where needed. The ability to deposit self-expanding material allows the MTR to achieve real-time climbing by creating its own support to overcome obstacles or bridge gaps. The proposed platform is also capable of depositing material accurately to perform effective damaged-structure reinforcement. Targeted material deposition has been implemented with multiple materials and this platform has been tested for applications to disaster scenarios. One such material is polyurethane foam, which allows easy deposition, expansion and solidification in fast enough time to enable the MTR to use it as a real-time support for climbing. The amount of foam deposited can be controlled and multiple layers can be stacked on top of each other to significantly increase altitude. The high compressive strength of the solidified polyurethane foam is sufficient for temporary support structures, or structural reinforcement allowing the MTR to operate in support of disaster relief workers. The MTR is also capable of depositing clay alongside polyurethane foam, making it able to repair damaged masonry and thus further improving its usefulness in more general maintenance and repair scenarios.
Harison Wara Che
City Chemist Roundabout, Cameroon
Title: Food security and nutrition trends in West Africa challenges and the way forward
Biography:
Harison Wara Che passionate about sustainable Development, Food security/processing, safety indigenous, Good living philosophies Environmental sustainability, Research theory and methodologies. His food philosophy is certainly called from years of experience in the industry and many adventures travelling, dining and meeting amazing people. However, it can undoubtedly be distilled to a concept I learned from the chef I truly confider my mentor Mike. While working in the industries in Cameroon my country of Birth I learned what is means to approach food with the mindset of a culinary anthropologist “and while working at the USA Army camp in Kandahar Afghanistan in a company called Supreme Group global food service his respect understand and appreciate the culinary tradon that underlie any particular foodstuff product or dish, Know how that ingredient is used in it indigenous form, then use that knowledge to apply it to whatever style or method suit you and joining organization that fight food was my biggest dream .
Abstract:
West Africa has experienced very little progress in reducing food insecurity and child malnutrition in the past 20 years. Approximately, one third of children under five years of age are stunted, and 5-15 percent is wasted. Micronutrient deficiencies, particularly lack of vitamin A, iron and iodine, affect mainly women and children and contribute to some of the highest rates of child mortality in the world. Overweight and obesity are emerging problems in some urban populations with negative implications for chronic non-communicable diseases. The causes of malnutrition and food insecurity are complex and include the agro-ecological, socio-economic and demographic characteristics of the sub-region. Rising incomes, rapid population growth especially in urban areas, desertification, as well as HIV/AIDS affect the food system. Changes in diets and lifestyles especially in urban settings involve a shift from the consumption of traditional staples to imported cereals (wheat and rice). Although food availability has generally improved in the sub- region, the dietary energy and protein supplies are still below requirements and unstable, especially in Sahel countries. The nutritional quality of local diets remains low for most people and access to adequate food is not always secure for the poor. Besides the need to diversify and increase food production and productivity, increased support is needed for appropriate food storage, processing, and preservation techniques at community and industrial level, and better distribution and marketing. Technologies, such as fortification and plant breeding, are increasingly relevant within a comprehensive food-based strategy. Nutrition education is a complementary activity for ensuring the effectiveness of food-based approaches. Based on a review of lessons learned from food-based interventions implemented by FAO and other development partners, this paper addresses some of the major issues, challenges and opportunities involved in fulfilling the pledge of West African countries to meet the goal of reducing malnutrition by 50 percent.
Samir Ladaci
National Polytechnic School of Constantine, Algeria
Title: Fractional order cruise control strategies for an electric vehicle
Biography:
Samir Ladaci has graduated in Automatics Engineer from the National Polytechnic School of Algiers in 1995 and received his Magister degree from Annaba University, Algeria, 1999. He obtained his PhD and HDR degrees from Mentouri University of Constantine, Algeria in 2007 and 2009 respectively. He is a Full Professor with the National Polytechnic School of Constantine and the Head of Control Research Team at the SP-Lab Laboratory, Constantine. He has more than 110 publications and supervises many PhD theses. His current research interests include fractional order systems and control, fractional adaptive control, robust control, systems identification and nonlinear control systems.
Abstract:
Fractional order controllers are gathering more and more interests from the control community for their ability to enhance the system control quality performances and robustness. In this work we are investigating different fractional order control strategies for the cruise control of an electrical vehicle. We will use a fractional order model reference adaptive control (FOMRAC) algorithm, an optimized fractional order PID controller (FOPID) and a fractional order high gain controller to improve the vehicle behavior in presence of disturbances and uncertainties. We introduce new tuning parameters for the closed-loop system performance improvement. A numerical simulation of an application study for cruise control of an electric car is proposed. Electric vehicles (EVs) are becoming more popular these days and automobile manufacturers are introducing various types of EVs in the market. The main advantages of EVs are the emission elimination, low operating cost, high efficiency, simplicity and superior controllability over the power train. The EV power train consists of an electric motor, single or double speed transmission and the final drive unit. Our fractional adaptive control algorithm is applied to the cruise control of a DC motor driven electric vehicle. This system is developed for driving with constant speed on long stretched roads. We show through computer simulations that it is able to compensate the disturbances from the road grade and changes in the vehicle weight. The results illustrate the effectiveness and robustness of the proposed algorithm.
- Design Engineering | Industrial Design | Manufacturing Process | Materials Science | Mechatronics Robots Applications of Automation | Human Robot Interaction | Control Systems
Location: Scala
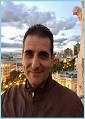
Chair
Jose M Pardor Gortor
The University Carlos III of Madrid, Spain
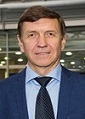
Co-Chair
Michal Krzyzanowski
Birmingham City University, UK
Session Introduction
Johanna Ender
Liverpool John Moores University, UK
Title: Design of an intelligent workplace system for human-machine-interaction in the digitized industry
Biography:
Johanna Ender passed her graduation as a Diploma Designer (FH) for Product Design (2017) with distinction from the Hochschule Wismar University of Applied Sciences Technology, Business and Design. She has started her international and interdisciplinary PhD research in June 2017 at the Faculty of Engineering and Technology of Liverpool John Moores University in cooperation with the Hochschule Wismar University. She received the Gottlob Frege Price 2017 for her final thesis, which was developed in cooperation with the Fraunhofer IGP, Rostock (Germany). A study project about a robot integration into a kitchen furniture was awarded with the Anja Schaible Price 2017 at the Living Kitchen (event), Cologne (Germany). She spent a pre-study practical in Tasmania. While studying, she developed a patent for a household appliance (DE 102015210996A1) for the Corporate Brand Siemens/Design of the BSH Hausgeräte GmbH within an internship. For her work as a designer, she was awarded as German Design Award Nominee 2018.
Abstract:
Modern industry workplaces include operators working intensely using computers, robots and autonomously operating machines. Tasks including human-machine interaction (HMI) are increasingly integrated into the work process. The work ranges of robots and operators in manual assembly and maintenance are progressively fusing – the coexistence will move towards human-robot collaboration (HRC). Consequently, the higher dynamics of processes in the digitized industry include additional stress factors and offers new challenges: HMI can result in cognitive overload of the worker due to the interpretation of multiple signals and therefore lead to a high risk of exhaustion. Furthermore, there are strong barriers to working with a robot colleague. To increase the acceptance of HRC and to reduce the strain of the worker, user-centered needs have to be sufficiently considered. However, workplaces for HMI are widely developed from a technology-centric perspective. The design research will close this gap by developing a novel holistic method for the design of industrial workplaces. Accordingly, the study places great emphasis on understanding of human factors in terms of its physical, cognitive and organizational limitations and their applications to industrial design. The workbench system includes a novel interface directing working tasks to the worker within the networked plant. Derived from the existing Pick-by-Light framework – where operators are directed to particular stock areas via light signals – the approach, named Work-by-Light, utilizes light displays to support the operators solving particular working tasks in collaboration with a robot. In particular, areas of interaction, like the supply and removal of work pieces through the robot, are highlighted as well as instructions for the assembly are communicated. Light signals inside the surface of the table are reduced to the minimum of information to support the rapid processing of the instruction through the worker. Consequently, the intuitive utilization of the interface reduces strain in HRC. It will be exemplified how the system can support the worker during maintenance and manufacturing of airplanes. Therefore, explorative testing of a conceptual prototype by potential users is planned.
Tobias Masiak
Zentrum für Mechatronik und Automatisierungstechnik gemeinnützige, Germany
Title: Implementation of a human-machine-interaction control system in a human-robotcollaborative riveting process in aircraft assembly
Time : 14:25-14:45
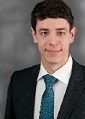
Biography:
Abstract:
Assembly processes in aircraft production are difficult to automate due to technical risks. Examples of such technical challenges are small batch sizes, large product dimensions and limited work space. Full automation of complex processes is expensive as it requires much effort with respect to service and maintenance. A semi-automated process, utilizing human-robot-collaboration, is the most effective approach for optimizing aircraft production in relation to aircraft section assembly. In the assembly process of the aft section of aircrafts, the pressure bulk head is assembled with the section barrel using hundreds of rivets. This assembly process is a non-ergonomic and demanding task in which two people are working together collaboratively. Working conditions can be improved through collaboration between the operator and the robot system. The approach is based on the process requirements as well as dynamic and skill based task sharing between the operator and the robot. This is demonstrated by positioning a robot within section 19. The robot's task is to position the anvil tool, while the operator performs the more complex task of inserting the rivet and operating the riveting tool. An intuitive operating is implemented to increase operator acceptance and to enable interaction with production equipment. Within the framework of natural and intuitive human machine interaction, smart devices are integrated to control process specific production equipment. Graphical user interfaces in smart phones or smart watches and the integration of mixed reality technology offers new possibilities for visualization and assistance. The developed systems allow intuitive configuration and operation of the station using an open control concept and dynamic task sharing. The operator is therefore supported with a collaborative robot in combination with additional assistance systems in order to improve production quality and ergonomics during the riveting process. The results are part of the EU’s Horizon 2020 research and innovation programme in the four by three projects at ZeMA.
Biography:
Carmine Pirozzi graduated with Honors in Industrial Engineering in 2004 with a PhD in Systems and Technology of Production. He is a Researcher in additive manufacturing since 2011, involved in projects as HYPROB, TIMA-RITAM, ANGELA, SAT-AM as material science and additive manufacturing engineer specialist. He does cooperate with several research centers, universities and firms being authors of more than 10 scientific articles on specialized journals and conferences.
Abstract:
The electron beam melting (EBM) is one of the most promising ALM technologies, which utilizes a high-energy electron beam, as a moving heat source, in order to melt and fuse (by rapid self-cooling) metal powder and produce parts in a layer-building fashion. Anyway many technical aspects concerning the quality of EBM produced components are still industrial open items and studies need to be carried out. The objective of this study is to evaluate the distribution and the features of porosity defects generated during the EBM process by using tomographic analysis, at this aim a simple test case, consisting in rectangular parallelepiped (50x10x10 mm) samples manufactured in Ti6Al4V, was chosen. A suitable DOE was developed in order to investigate the effect of the following intra-build process parameters on porosity: Samples orientation: samples were built according to n.4 different orientations: x, y, z (90°) and 45°. The x and y oriented samples were built horizontally and they were, respectively, parallel and perpendicular to the rake movement direction and the 90° oriented samples were built vertically. Height in the build chamber: the group of samples shown in 2b was built at n.3 different levels in the build chamber which are named hereafter: h1, h2 and h3. More in detail, h1 level starts at z=40 mm, h2 level starts at z=170 mm and h3 level starts at z=300 mm.
Zaheer Abbas
National University of Science and Technology, Pakistan
Title: Design optimization of spot welds for optimal strength of structure
Biography:
Zaheer Abbas pursued his BE in Aerospace from College of Aeronautical Engineering at the National University of Engineering & Technology in 2010. He is currently pursuing MS in Aerospace Engineering from National University of Engineering & Technology.
Abstract:
Resistance spot welding (RSW) is particularly employed for high volume and rapid welding applications in automotive assembly process for joining multiple metal sheets and parts. The failure of spot welded joints are linked to several factors like, weld nugget size, edge distance, spacing between spot welds, sheet thickness, material properties of heat affected zone, residual stresses and material inhomogeneity. Finite element analysis (FEA) of multiple spot welded joints under tensile-shear load are investigated to attain optimum strength and desired factor of safety. The analysis shows that spacing between the adjacent spot welds, edge distance and thickness of the sheets are primary factors affecting the strength of the joints for a given material. The optimal edge distance increases the strength of the weld by providing clearance of spot welds from plate edge. The optimal spacing of spot welds is the thin line between the stress superimposition and supporting effect of spot welds. The variation of sheet thickness effects the strength of spot welds as the optimal edge distance changes with thickness. For asymmetric thickness of sheets, strength is defined by thinner sheet and for symmetric sheet edge optimal edge distance varies with thickness.
Grazvydas Kazokaitis
Kaunas University of Technology, Lithuania
Title: Spherical magnetic drive for attitude control on nano satellites

Biography:
Grazvydas Kazokaitis has experience in design and R&D fields developing small and precise mechanisms for ultra-fast laser beam control and machining apparatus. This experience allows providing solid foundation and knowledge creating possible solutions for laser beam orientation mechanisms between small units in space, attitude control and other control tasks.
Abstract:
Small satellites are great tools for various research and analysis tasks. They can work like standalone units or to be modular and combined together to the clusters. Depending on their missions and provided exercises, various orientation and positioning systems are needed. Attitude control systems can be with active or passive elements. Typically, these systems are driven by: gravitational forces, permanent or electromagnets, reactions wheels or thrusters. Small satellites have limited capabilities and many restrictions for size, composition, energy consumptions. Nowadays most popular systems consume significant amounts of energy, takes a lot of volume. As a possible option for alternative attitude control mechanism spherical magnetic drive was submitted. Spherical permanent magnet has stable dipole and when it orientates with the Earth’s magnetic field, attitude control can be achieved. This developed drive combines advantages of active and passive systems. The drive is fairly simple: permanent magnetic sphere is inserted between two ring-shaped piezoelectric actuators. Electrodes of the piezoelectric rings are divided into three equal sectors and are excited by separate harmonic signal. The out-of-plane bending and radial vibration modes of the piezoelectric rings are excited to obtain elliptical motion of the contacting points and rotate magnetic sphere about three axes. Amplitude and duration of the applied signal depends on rotation or motion trajectory of the sphere. In addition, it must be mentioned that actuator can be driven by burst type signal in order to achieve very high resolution. Using this technique, controlled movement of magnetic sphere is achieved. Numerical and experimental studies were performed to verify operating principle and output characteristics of the actuator. The aim of study was to investigate vibration modes of the piezoelectric actuators and identify resonance frequencies at which these piezoelectric actuators generate 3-DOF rotational motion of a spherical rotor with high resolution, determinate further development steps.